Safety & Health
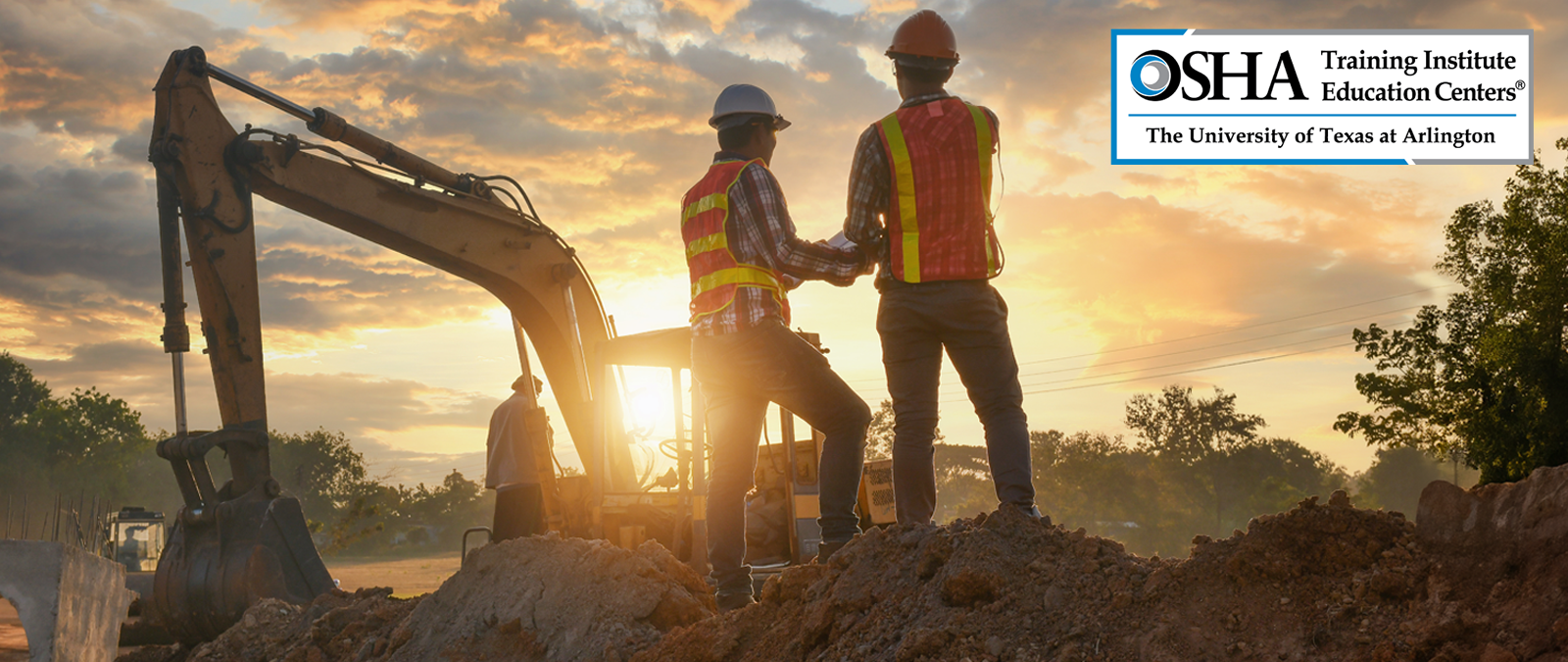
The OSHA Education Center at The University of Texas at Arlington stands as the premier OSHA Training Institute Education Center in the nation. As a distinguished leader in occupational safety and health training, we are dedicated to providing comprehensive education in the field. Our expert instructors, with extensive real-world experience, deliver training that adheres to the highest quality standards. Certification programs span various industry tracks, including General Industry, Construction, Oil & Gas, Risk Management, and more. With a focus on practical skills and compliance, our programs ensure a safer and healthier work environment while fostering career growth and opportunities.
Certification Programs
Upcoming Class
Course | Dates | Location |
---|---|---|
OSHA #500 Trainer Course in OSHA Standards for Construction | August 5-8 | Arlington, TX |
OSHA #2045 Machinery and Machine Guarding Standards | August 5-8 | El Paso, TX |
OSHA #2455 Safety and Health Management Program | August 12-14 | Willow Park, TX |
OSHA #2264 Permit-Required Confined Space Entry | August 12-14 | Albuquerque, NM |
OSHA #7400 Occupational Noise Exposure Hazards | August 18 | Arlington, TX |
SH 702 Accident Investigation Certificate Program | August 18-22 | Albuquerque, NM |
SH 321 NFPA 70E Electrical Safety in the Workplace | August 18-21 | Live Webcast |
OSHA #2225 Respiratory Protection | August 18-28 | Live Webcast |
OSHA #510 Occupational Safety & Health Standards for Construction | August 19-22 | Live Webcast |
SH 785 Root Cause Analysis | August 21-22 | Live Webcast |
Click here to view full course schedule.
Updates
2025 Ladder Safety Symposium
Each year, more than 500,000 people in the United States are treated for ladder-related injuries, with over 300 fatalities. In this informative session, experts from Little Giant will discuss the most common ladder safety issues found on worksites, provide practical solutions to prevent incidents, and share insights on best practices, proper usage, and industry trends to help reduce workplace injuries and enhance overall safety.
Tragedies in the Trenches Free Webinar | Oct 16, 2024
Presented in case study format, facts from events will be utilized throughout the session to dispel common myths as well as emphasize key takeaways for future safe work in excavations. Your host, Kimlee Lindgren, CHST, has decades of experience as an OSHA Training Institute Education Center Instructor in California, Hawaii, Nevada, Arizona, New England and the Midwest as well as a Cal/OSHA compliance officer. Kimlee has worked on over 50 fatality cases in her career including those in the excavations and trenches.
Focus Four - Health: High Temperatures
You are familiar with OSHA's Focus Four in construction, but you may not be familiar with the Focus Four four Health recently distributed by the American Industrial Hygiene Association (AIHA). The Focus Four Health are; Manual Material Handling, Noise, Air Contaminants, and High Temperatures.
Heat is a hazard during the summer, but it is not always taken seriously. This is a serious health threat and one where the effects occur during or shortly after exposure. An average of 30 workers die and thousands become sick every year from heat exposure. The past 16 years rank among the top 17 warmest years on record.
Control Strategy:
- Implement and check controls
- Heat Index forecast
- Adjust risk levels for risk factors such as full sun, work area, workload
- Tailor protective measures to risk level:
- Hydration
- Shade/cooling
- Rest/break schedule
- Work schedule
- Engineer controls/PPE
- Emergency planning and response
- Acclimatization
- Monitoring
Free Warehousing Safety Video Presentation
You might be surprised to learn that according to OSHA, warehouses are one of the most hazardous places of employment. But why is that? What is it about warehouses that can make them such a dangerous place to work? Warehouses and distribution centers are fast-paced, active environments– even more so with the exponential growth of eCommerce.
This Webinar developed by Region VI OSHA and the Region VI OSHA Training Institute Education Centers is intended to raise awareness among both workers and employers about the hazards in the industries covered under OSHA's National Emphasis Program on Warehousing and Distribution Center Operations. This includes warehousing centers, mail and postal processing and distribution centers, parcel delivery/courier services, and certain high injury rate retail establishments, which according to the Bureau of Labor Statistics data experience significantly higher injury and illness rates than other establishments. Warehousing and distribution centers have experienced tremendous growth within the past ten years. From January 2011 to December 2021, the warehousing and distribution centers industry experienced a surge in employment, increasing respectively from 668,900 employed to a total 1,713,900 employed. At the same time the warehousing and distribution center industry has experienced high occupational injuries and illness rates. During the five-year period from 2017 through 2021, the average incidence rate of nonfatal occupational injuries and illnesses for warehousing and services were significantly higher than the baseline private general industry rates.
This Webinar is intended to raise awareness among both workers and employers about these hazards and their associated risks. Early recognition and avoidance, in conjunction with abatement, will protect workers while helping employers to save money and improve productivity.
Introducing Digital Badging
The University of Texas at Arlington Division for Enterprise Development has partnered with digital badge provider, Credly, to offer digital badges at the conclusion of your course, certificate program or conference. You could earn a badge that would indicate your skills and accomplishments and then share the badge on various online platforms to showcase your achievement. Digital badges are micro-credentials that recognize a person's achievement, skill, or knowledge. Your digital badges can also be accessed by employers and other interested parties by clicking on the badge to verify the meta-data stored on the Credly badging platform that will contain the details regarding the badge micro-credential.
OSHA Offers New Resources to Promote Warehousing and Storage Safety
The warehousing and storage industry includes establishments operating facilities for general merchandise, refrigerated goods, and other products. These establishments may also provide logistical services relating to goods distribution. Potential hazards in this rapidly growing, fast-paced industry include those associated with powered industrial trucks (forklifts), ergonomics, material handling, hazardous chemicals, slip/trip/falls, and robotics. The most common injuries are musculoskeletal disorders (mainly from overexertion in lifting and lowering) and being struck by powered industrial trucks and other materials handling equipment.
OSHA's new Warehousing and Storage webpage provides information on avoiding common hazards, including operating forklifts and lifting, handling and storing materials.
Learn more about materials handling and storage hazards in our OSHA #511 Occupational Safety and Health Standards for General Industry and our OSHA #7005 Warehousing and Storage courses.
Falls to Lower Level Tops List of Costliest Construction Injuries
The top five costliest injuries in the construction industry in 2018 had a combined price tag of nearly $9 billion, according to the Liberty Mutual Workplace Safety Index - an annual ranking of serious, nonfatal workplace injuries based on direct workers' compensation costs involving more than five days away from work. Falls to a lower level was the costliest injury at almost $3.6 billion, followed by overexertion resulting from handling objects ($2.2 billion), struck by objects or equipment ($1.4 billion), falls on the same level ($990 million), and other exertions or bodily reactions ($670 million). Those five injury types made up around 84% of all injuries in construction for the year.
Learn how to prevent these costly incidents by attending one of our OSHA #3115 Fall Protection classes in-person or via live webcast!
Free Online OSHA Training Courses
Looking for some free short training courses on critical safety and health issues? These one hour training courses developed by Region VI OSHA and the OSHA Education Centers provide information on a variety of topics:
» Amputation» Healthcare Safety
» Ladder Safety Symposium
» Preventing Falls in the Workplace
» Protecting Workers in Oil and Gas
» Protecting Workers in Trenches
» Safe+Sound
» Safety Directors Talk About Safety Climate
» Silica: Every Breath You Take
» Tank Cleaning
» Warehousing
Other News
The Basic Steps to Prevent Falls in Construction: Plan, Provide, Train
Falls are the most common causes of serious work-related injuries and deaths on the worksite in construction. Each year in the U.S. more than 200 construction workers are killed and over 10,000 are seriously injured by falls. It is essential that employers set up jobsites to prevent employees from falling from overhead platforms, elevated workstations or into holes in the floor and walls. As OSHA highlights in its outreach campaign, falls can be prevented and lives can be saved through three important and highly effective steps: Plan, Provide and Train.
- PLAN ahead to get the job done safely: Employers must plan projects that involve working from heights to ensure that the job is done safely by deciding how the job will be done, the tasks involved and the safety equipment that may be needed to complete each task. CPWR provides a tool for developing a Fall Protection Plan.
- PROVIDE the right equipment: To protect workers who are six feet or more above lower levels, employers must provide fall protection and the right equipment for the job, including the right kinds of ladders, scaffolds, and safety gear. If workers need personal fall arrest systems (PFAS) for roof work, employers should provide a properly fitting harness for each worker who needs to tie off to an anchor and make sure the PFAS is worn properly and is inspected regularly.
- TRAIN everyone to use the equipment safely: Every worker should be trained to recognize hazards and to properly set-up and safely use equipment required for his/her job. OSHA has provided numerous materials and resources to train workers on safe practices to avoid falls in construction.
Learn how to prevent falls on your jobsites by understanding the hazards and developing a thorough fall protection plan, providing the right equipment, and training your workers on hazard awareness and the proper use of safety equipment by taking one of our OSHA #3115 Fall Protection classes.
Confined Spaces - Overlooked Hazards
Many workplaces contain “confined spaces”, while not designed to accommodate people, these spaces are large enough for workers to enter and perform certain required tasks. A confined space is not designed for human occupancy but is large enough and configured so a worker can bodily enter and has limited or restricted openings for entry or exit. When the potential for a hazard exists in this space, it becomes a permit-required space governed by specific OSHA standards. Typical confined spaces include tanks, storage bins, vaults, pits, manholes, tunnels, ductwork, and pipelines. Many employers are not aware of their responsibilities under OSHA's General Industry Permit-Required Confined Space Standard regarding workers who are exposed to the hazards of confined spaces. Employers must identify all potential hazards, develop written safety and rescue procedures, and provide training and protective equipment to workers to eliminate or greatly reduce the risks of working in confined spaces and to maintain full OSHA compliance. Learn more on OSHA's Confined Space webpage.
OSHA published the Protecting Construction Workers in Confined Spaces: Small Entity Compliance Guide to assist employers and workers in understanding their requirements under the Confined Spaces in Construction Standard. This 57-page guide covers a wide range of topics, including employer responsibilities, overview of the standard, identifying permit spaces, worker training, rescue and emergency services, and permit-required confined space program and entry permit samples. See also OSHA's Confined Spaces in Construction webpage.
Want to learn more? Check out our upcoming OSHA #2264 Permit-Required Confined Space Entry classes.
Excavation and Trench Safety
Each year, construction workers are injured or killed when the walls of the trench they are working in collapse. One cubic yard of dirt can weigh 3,000 pounds or more. As a result, survival time in a collapsed trench can be as little as a minute if the victim is buried and there are no air pockets. This means that sometimes, not even immediate rescue can save the victim. Trench collapses and cave-ins are a serious threat to workers, but they can be prevented.
- PREPARE a safe trench. - Provide safe entry and exit before starting work. - Keep materials at least 2 feet away from the edge.
- PROTECT workers from a cave-in by using protective systems. - Sloping or benching trench walls, or - Shoring trench wall with supports, or - Shielding trench walls with trench boxes.
- INSPECT the trench for hazards. - Look for standing water and other environmental hazards. - Never enter a trench unless it has been inspected and approved by the competent person.
OSHA has made reducing trenching and excavation hazards the Agency's Priority Goal. To learn more, enroll in next OSHA #3015 Excavation, Trenching, and Soil Mechanics course.
Region VI OSHA Enforcement Initiative Targets Tank Cleaning Operations
Effective July 23, Region VI OSHA launched a new enforcement initiative to target transportation tank cleaning operations in Arkansas, Louisiana, Oklahoma, and Texas. Workers employed in the industry face many hazards that can lead to serious injury, illness, and death, including fire, explosions, hazardous atmosphere, and hazardous chemicals. The targeted industries include:
- NAICS 484110: General Freight Trucking, Local
- NAICS 488210: Support Activities for Rail Transportation
- NAICS 488490: Other Support Activities for Road Transportation
- NAICS 488510: Freight Transportation Arrangement
- NAICS 562910: Remediation Services
- NAICS 562920: Materials Recovery Facilities
- NAICS 562998: All Other Miscellaneous Waste Management Services
This initiative provides OSHA enforcement officers the authority to evaluate the employers' workplace(s) at all programmed, unprogrammed, or other limited-scope inspections pertaining to transportation tank cleaning operations to assure that employees are being properly protected.
Region VI OSHA and OSHA Education Centers have partnered to prepare a free webinar to assist companies in understanding the hazards and the controls. Outreach, consultation services, and training will be provided to affected employers as requested.
"Take 3 in 30" Challenge
Management leadership is a core element of a workplace safety and health program. Accelerate your program and show your commitment in your workplace. 3 in 30! Here's how you do it:
- Take 3 actions in 30 days
There are lots of ways to accelerate your program! Choose from our list or pick one of your own. Every workplace is different so select actions that work best for you. - Share in your workplace
It is important for your employees to see your commitment to safety! Show them that safety starts with you! List your three actions and share it on social media, in your company newsletter, or post it in the workplace. - Accept your challenge coin
You did it! Visit our website once you complete your activities to download your virtual challenge coin for showing Management Leadership. Share it on social media, post it in your workplace, or put it in your signature file – display it proudly!
Download the Take 3 in 30 Challenge and share in your workplace and on social media!